Article: Design of Lackawanna's Reinforced Concrete Freight Terminal Warehouse at Jersey City. Published in The Engineering News-Record, March 27, 1930.
2012.001.0217
2012.001
Purchase
Purchase
Museum Collections.
1930 - 1930
Date(s) Created: 1930 Date(s): 1930
Notes: Archives 2012.001.0217 ==== ENGINEERING NEWS-RECORD March 27,1930 519 --- Fig. 1—Model of Lackawanna's Freight Terminal Warehouse and Flat-Slab Track Viaducts --- Design of Lackawanna's Reinforced Concrete Freight Terminal Warehouse at Jersey City Eight-Story Structure, 848x162 Ft., Flanked by Flat-Slab Viaducts Carrying Tracks and Truckways—Part of Extensive Terminal Development By M. Hirschthal Concrete Engineer, Delaware, Lackawanna & Western R.R., Hoboken, N.J. TO PROVIDE facilities for temporary storage of goods in transit intended for export or for future delivery into New York City, the Lackawanna Railroad is constructing an extensive freight terminal at Jersey City, including a modern eight-story reinforced-concrete warehouse, located a short distance from its Hoboken passenger terminal. The project includes extensive track revision, both siding and drill tracks, the construction of a pier on the Hudson River front, the removal of an existing engine house and the construction of a new one to replace it, and four individual bridges over streets either extensions to present bridges or at independent locations, besides the main warehouse and freight building and its immediate facilities. The proximity of the warehouse to the New Jersey entrance of the Holland tunnel makes it available and convenient for shippers of goods destined for New York. A track from the warehouse to the new pier will facilitate the movement of goods destined for export or lighterage. The freight terminal and warehouse include a main building 848 ft. long by 162 ft. wide, consisting of eight stories and a basement, with a three-track concrete flat-slab viaduct along the south side having a length of 1,463 ft. and another viaduct of similar design along the north side the full length of the building, accommodating five tracks and an intervening loading platform and driveway. Both viaducts are joined to the building at the second-floor level with platforms for loading to and from the building proper, while other building facilities are provided underneath the track slabs of both viaducts. Fig. 2 shows general plans and details of the terminal. Aside from the immensity of the project, this warehouse is interesting in its design. The design problems of the warehouse building are entirely different from those encountered in the adjoining viaducts, because of the character of the loading, its intensity and amount. They have, however, this in common—they are all of the gir-derless flat-slab type, the building of the two-way and the track slabs of the four-way system of reinforcement. The column layout for both the building and the viaducts is on the basis of 25x25-ft. square panels, the only exceptions being the street intersections and the expansion joints, this spacing being somewhat simplified by the closing of Erie Ave. and of Seventeenth St. Viaduct Design South Viaduct—The viaduct on the south side accommodates three tracks 124- ft. on centers, so that each outside track is located over the respective center line of columns. This design is unusual in that there is no continuity transversely, which continuity ordinarily would tend to reduce the moments in the slab. This, however, is compensated for in the overhang on either side. On the building side there is a platform supported by a curb wall at the edge of the track slab forming a concentration along that line. On the street side (Sixteenth St.) the edge of the track slab, which overhangs a distance of 9 ft. 9 in. beyond the center line of columns, is surmounted by an ornamental concrete balustrade. This viaduct extends beyond the present building limit at Grove St. to beyond Henderson St., and the length between Grove and Henderson Sts. on the building side is provided with a low curb wall surmounted by an iron railing so that if another unit of the warehouse is ever built along the viaduct the railing may be removed and the curb built up to the platform level. Though all the bridges on the Lackawanna Railroad are designed for an E-65 engine loading, it was not deemed necessary to design the viaducts for the heaviest road engine loadings, as slow movements will prevail over these structures. An E-60 loading was used with an impact allowance of 25 per cent rather than the full impact derived from the usual formula: Live Load I = __________ x Live Load Live Load + Dead Load The thickness of slab required for the above conditions is 24 in., with an additional thickness of 10 in. for the 10-ft. square drop-panels. The columns are 3 ft. in diameter, reinforced with vertical bars and spiral hooping. The footing design is rather unusual. Borings had [end pg 519] ==== 520 Figure 2 General Plans and Details of Warehouse and Viaducts [end pg 520] ==== 521 FIG. 3—SOUTH VIADUCT AND SECOND FLOOR OF WAREHOUSE Contractor's concrete plant in background. ---- been taken and plotted for the entire area of the improvement. Concrete piles were selected for the foundations of the viaducts in preference to timber piles, because they permitted a higher cutoff (El. +2.5) and a narrower footing. Ordinarily such footings would be designed as individual foundations for each column, or a transverse combination for each row of two columns. But by placing a continuous footing under each longitudinal row of columns the foundation was designed for a maximum condition of loading for the full section between the expansion joints. Had individual footings or a foundation at each bent been used, each footing would have had to be designed for the maximum reaction that may be obtained at the bent. The design selected resulted in considerable economy in the number of piles required, as well as in the amount of concrete and excavation. The maximum permissible loading on the concrete piles used in the design was 30 tons per pile. Across Grove and Henderson Sts. the footings were designed as continuous transversely, parallel to the center line of the street, because of various pipe lines encountered. At Henderson St. the pipes were placed in a concrete box hung from the footing of the columns along the street center line, the space between piles forming a pipe gallery. North Viaduct—On the north side of the building a much wider viaduct is provided to accommodate five tracks and a driveway. The total width of this viaduct is 117 1/2 ft., consisting of four 25-ft. panels with 8-ft. 9-in. overhangs on each side. Similar to the south viaduct there is a loading platform at the level of the second floor of the building. At the east end of the viaduct is a temporary precast concrete crib abutment to provide for future extension. Except for width, the north viaduct is identical in design to the south viaduct, the difference in moments in the deck slab being compensated for by the amount of reinforcement provided. Because of the widths of the street for both Henderson and Grove Sts. the column centers at these crossings were made 27 ft. center to center, with an expansion joint at the sidewalk spans. The other expansion joints in the viaduct are located about 250 ft. apart to correspond to those in the main building. The design of the track slabs was based on the methods used in this office for all girderless flat-slab bridges, the maximum positive and negative moments being found and distributed in accordance with design methods as described in the article on the Hackensack River bridge and its concrete approaches, Engineering News-Record, May 17, 1928, p. 779, except that the loading is as indicated above. Both viaducts are being waterproofed with a two-ply membrane of asphalt-saturated cotton cloth laid in asphalt, protected by asphalt blocks on the horizontal surfaces and brick along vertical parapets and platform curbs. The expansion joints for these viaducts, similar to those for other Lackawanna structures, are made by completely cutting the structure at cantilevers from the adjacent columns, the opening being spanned by bent sheet copper fitted into raggles on top of the slab, raised above the slab level to shed water. The joint is then waterproofed in the same manner as the remainder of the structure. Main Building Design Unusually heavy live loads, considered as uniform, were used in designing the main building; 350 lb. per sq.ft. for the basement, first and second floors, 300 lb. for the third and fourth floors, and 250 lb. for the fifth, sixth, seventh and eighth floors. In addition to these loads, four columns carry the load of a 60,000-gal. water tank. Even though advantage was taken of the provision for reduction of live loads for multiple stories, permissible under the Jersey City building code (identical with that of New York City), the maximum column concentration on the basement columns is 2,750,000 lb. Foundations—Because of the heavy column loads, the original design of the foundations called for open caissons carried down to rock. In construction, however, it was found that the steel sheeting for these caissons was difficult to drive because of boulders encountered; therefore the type of foundations was changed to individual concrete footings on concrete piles surmounted by a con- [end pg 521] ==== 522 tinuous reinforced-concrete mat over the whole area to form the basement floor. Piles for the main footings were cut off at El. —9.42, the top of the basement floor being El. -—3.5. To avoid expensive excavation that would have been necessary by carrying the entire footing and pedestal below the floor surface, the pedestals were permitted to protrude above the basement floor level to provide for the tremendous punching shear resulting from the heavy column concentrations. All the foundations are reinforced in both directions, except the combined footings between the pairs of elevator shafts, which required a special design. Columns — To carry the maximum load of the basement columns, 2,750,000 lb., required a concrete column section 4 ft. 4 in. in diameter, spirally and longitudinally reinforced with the maximum amount of reinforcement, consisting of 25 1-1/4-in. square bars and 3/4-in. round rod hooping with 2-in. pitch. In the basement a column of this diameter was permitted, but for the stories above the ground level a maximum diameter of 3 ft. 4 in. was not to be exceeded. Therefore, for the interior columns of the first and second floors a composite column was used, consisting of a structural steel core of 14-in. H-sections with added plates where required, in a 3-ft. 4-in. concrete column additionally reinforced with spiral hooping and longitudinal rod reinforcement, all set on a steel billet to transfer the loads to the basement columns. Above the second story it was possible to use columns reinforced only with rods and spirals, the column diameters varying from 3 ft. 4 in. in the third story to 20 in. for those supporting the roof. Walls — The basement walls are designed as reinforced-concrete retaining walls with main reinforcing running horizontally between the wall columns, which act as counterforts for the wall slab. The walls for the upper stories are brick veneer with concrete block backing, each tier being supported by the overhanging concrete floor slab. The first plan for waterproofing the basement contemplated the use of a three-ply membrane waterproofing on a concrete protection coat, but because of fear that this could not be installed under the existing water pressure, a plastic waterproofing coat was decided upon to be laid on top of the basement floor and carried up the sides of the walls and columns. ---- FIG. 5 — GENERAL CONSTRUCTION VIEW North viaduct and concrete plant in background. First-floor forms for building in foreground. Filedriving and foundation work at extreme left. ---- FIG. 4 - FOUR-WAY REINFORCEMENT ON NORTH VIADUCT DECK ---- The basement story height was fixed at 10 ft., but the height of the first story, dependent on the elevation of the loading platforms at the second-floor level, which results from the 14-ft. underclearance at Grove and Henderson Sts., is 21 ft. 5-1/2 in. over the driveway. A feature of the building is the truck-loading platforms elevated 3-1/2 ft. above the driveway, arranged sawtooth in plan (Fig. 2), permitting room for through traffic for trucks as well as for loading and delivery space. The height of all other stories is 11 ft. from floor to ceiling, except the top story, where the maximum height is 12-1/2 ft. The floor panels in the building are 25 ft. square with a 6-ft. overhang on the sides and ends of the building. There are eleven bays in each end section and ten bays in the center section separated by expansion joints at which the columns are spaced 17 ft. on centers. Transversely there are six bays. The building is divided into six units by concrete fire walls to reduce the fire hazard, and an automatic sprinkler system is installed throughout. For the two-way flat-slab system which was adopted as the type of floor for the building, the slab thickness required for the first and second floors is 1 ft. 1/2 in., for the third and fourth floors 1 ft. and for the upper floors 11 1/2 in. The drop panels were made 6 in. deep in all instances for uniformity. In the vicinity of the elevators special designs were necessary because of. the concentrated loads to be carried and the break in the reinforcement bands caused by the elevator openings. This, of course, could not be designed by code coefficients, the moments and shears being computed from actual loads. In these special cases, instead of resorting to beams, the drop panels were made continuous for the panels in which the elevators occur, [end pg 522] ==== 523 resulting in a total slab thickness in those sections varying from 1 ft. 6-1/2 in. on the lower floors to 1 ft. 5-1/2 in. on the upper floors, while a thickness of 1 ft. 6 in. was required on the roof slab because of the weight of the elevator machinery which had to be carried there. The basement floor slab was designed both for the downward live load of 350 lb. per sq.ft. and for the upward water pressure to which it would be subjected. A total of 26 elevators is provided, distributed on both sides of the building, to be available from the main driveway platforms as well as from the outside platforms under the viaducts. Two of these are passenger elevators located at each end of the building, the remainder being freight elevators, four of which are exceptionally large, 22 ft. 1-3/4 in. x 9 ft. 4 in., for the accommodation of automobiles. A notable feature of the design of this building is the fact that despite the numerous openings for elevators, stairs, ventilating shafts, ducts,, etc., not a single beam projects below the ceiling level, except for the fire stop above the driveway, thus greatly simplifying the formwork. The wearing surface of the floors throughout the building, above the basement, with the exception of the paved driveway on the first floor and the floors of the toilet rooms, consists of a patented 1-in. cement finish. Because of the great length of the driveway through the building, it was deemed advisable to install a ventilating system, which consists of compressor fans located under the second-floor level and ventilating ducts through all the floors and the roof to carry the foul air out of the building. The main power cables, running lengthwise of the building, are carried in electric conduits in the space between the sawtooth platform and the driveway slab of the first floor. The electric power is supplied by two banks of transformers, each composed of three single-phase 150-kva. transformers located in the basement transformer vaults, while the motors for the elevators are supplied power (three phase, 60 cycles, 440 volts) by means of three single-phase transformers located on the eighth floor. A 60,000-gal. water tank is carried above the roof, supported on four of the building columns, and will supply water for sprinkler system, sanitary service and standpipe. A 4-ft. steel smokestack 140 ft. high, incased in brick and lined with firebrick, is carried on a beam spanning between footings supporting two of the build- ---- Fig-. 6 — TYPE OF CONCRETE CRIB RETAINING WALL USED TO HOLD FILLS ---- Fig. 7 Cross-Section of New Pier 10 ---- ing columns. This stack is built in connection with the incinerator, which consists of two units 9x20-1/2 ft., fed by chutes 4 ft. square, and is also connected with hot water heaters. The space under both the north and the south viaducts is designed for building purposes, being provided with driveways and loading platforms for vehicles, both sections being directly connected with the building proper. Other Terminal Features—Besides the viaducts and the main building there are other features connected with the terminal and forming a part of the continuity of the whole layout that are also interesting. Among them is the pier at the riverfront, which gives the warehouse and freight terminal a direct connection with the Hudson River. This pier, known as Pier 10, is more than 1,000 QUANTITIES IN ENTIRE TERMINAL IMPROVEMENT Concrete piles in track viaducts, lin.ft................. 147,000 Concrete piles in building foundations, lin.ft............ 195,000 Concrete in track viaducts, cu.yd..........................................25,000 Concrete in building, cu.yd......................................................80,000 Concrete in abutments, walls and piers, cu.yd....................5,200 Reinforcing steel in track viaducts, lb..................................3,700,000 Reinforcing steel in building, lb....................... 14,000,000 Structural steel in column cores, lb......................................2,4 60,000 Structural steel in bridges, lb..................................................1,370,000 Number of units in concrete crib wall................................32,500 ft. long, is 38 ft. wide and carries two tracks. The construction of the pier consists of wooden piles surmounted by a solid timber floor at low-water level, the sides and ends carrying heavy concrete retaining walls which hold a cinder fill carried to subgrade (Fig. 7). Base of rail elevation on this pier is El. +8, the same as that through the freight yard. The track is then carried on an ascending grade between precast concrete crib walls (Fig. 6) on a 1 per cent grade for 1,700 ft., and 500 ft. at 0.5 per cent grade to the Henderson St. bridge, reaching El. 25.50, the viaduct track level. The Henderson St. bridge is a single-track through-girder bridge supported on steel columns at the curb line and on concrete abutments at the street line, with a solid concrete deck. Three other bridges in the terminal improvement are additions to present structures, one at Grove St., one over the Erie Junction Railroad, and one at Hoboken Ave., which, because of a skew, requires 117-ft. plate girders, each weighing 70 tons. The concrete piers for this bridge, along the curb line, are of the open arch type, and because of the extreme skew and the various conditions of loading are subject to complicated stresses and are designed as hollow girders of the complete depth of pier to distribute the foundation loads. Prior to the detailing of plans for this project a wooden model of the structure and one of the entire layout were made for the purpose of demonstrating the feasibility of the project and illustrating its various details, shown in Fig. 1. Concrete Specifications—The specification for all the concrete on this project was based on the water cement [end pg 523] ==== 524 ratio, 2,500 lb. concrete with 6 1/4 gal. of total water per bag of cement for the reinforced concrete, and 2,000 lb. concrete with 6 3/4 gal. of water for the mass concrete. Four test specimens are made from each pour, two of which are tested at the end of 28 days, the other two at the end of 60 days. The time of mix and the amount of water are continuously watched to insure the proper resulting concrete and the test cylinders have given a uniformly good check on the quality of the concrete required. Contractors and Personnel — The design and construction of this whole project are carried on under the general direction of G. J. Ray, chief engineer of the Lackawanna. The design is under the supervision of J. L. Vogel, bridge engineer, and the writer, while the construction is under the general supervision of M. H. Doughty, division engineer, with W. L. Lozier as resident engineer. The architectural work is under the supervision of D. T. Mack, architect of the railroad company. The Turner Construction Co., New York, is general contractor on the viaducts, bridges and warehouse. The Raymond Concrete Pile Co. was subcontractor on the foundation work. The concrete crib retaining walls, grading and trackwork are being handled by railroad forces. [end of article] ==== ==== Status: OK Status By: dw Status Date: 2012-12-12
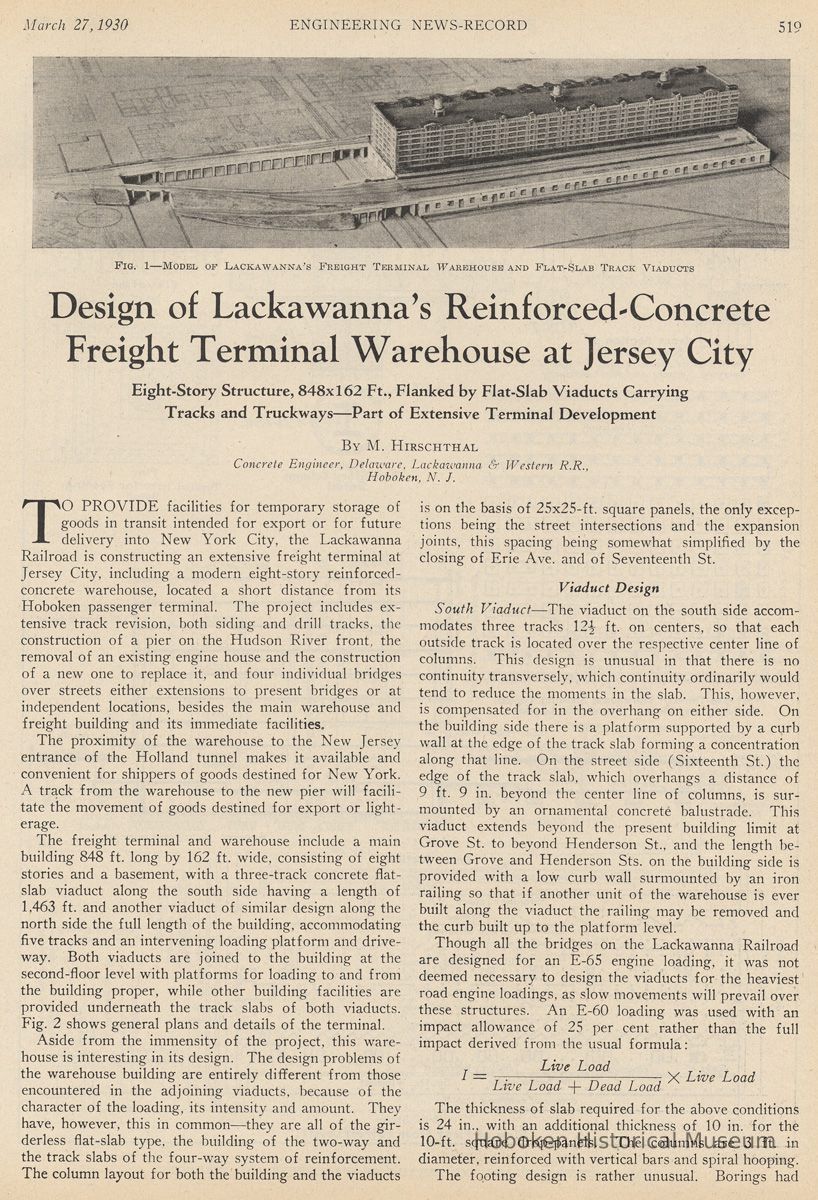