Article: Coffee Roasting Plant in Hoboken. Published in Engineering News-Record, Oct. 26, 1939, pp. 73-75.
2012.001.0182
2012.001
Purchase
Purchase
Museum Collections.
1939 - 1939
Date(s) Created: 1939 Date(s): 1939
Notes: 2012.001.0182 ==== ENGINEERING NEWS-RECORD October 26, 1939 (Vol. p. 559) 73 ==== [caption for Fairchild Aerial Photo at top of page] Fig. 1. New plant for Maxwell House Coffee, looking north [cataloger's note - view is actually northeast] across the riverfront site. --- Coffee Roasting Plant in Hoboken Contents in Brief —- Largest and most modern coffee plant in the world receives coffee off the boat in sacks and ships it, ready for use, in cans made on the premises. Five buildings are steel frame and two of reinforced concrete, flat-slab construction; all are on concrete piles. Live loads vary from 250 to 2,000 lb. per sq. ft. on concrete floors in which several thousand inserts for machinery had to be placed. Piles under 50-yr.-old pier support new shed. --- Consolidation by General Foods Corp. of widely scattered coffee processing operations and research activities in a new plant on the Hudson River waterfront in Hoboken, N. J., opposite New York City, gave rise to one of the outstanding building operations of the year. Seven separate buildings have been built on a 9-acre tract of made-land formerly occupied by railroad yards. Supported on concrete piles, and of both reinforced concrete and steel construction, the buildings, both single and multi-story, provide a floor area of about 500,000 sq.ft. which accommodates the most modern equipment for handling, mixing, roasting and packing 600,000 lb. of coffee daily. Grouped in a square, as shown in Fig. 1, the buildings are respectively the pier shed, the storage building, the processing building where Maxwell House coffee is blended, roasted, ground and packed, the extraction building where caffein is removed from the beans used for Sanka and Kaffee Hag coffees, the power house, the laboratory and the can factory. Excepting the pier shed and storage unit, whose walls are of cement-asbestos sheets, all buildings are faced with buff iron-spot face brick in bands that alternate with bands of steel sash continuous around the corners, this particular brick being chosen to match that used in the approach structures of the nearby Lincoln Tunnel; in all, 2,000,000 brick and 71,000 sq.ft. of sash and glazing are required. Sills and copings on all buildings are of precast concrete. The plant was designed and built by the H. K. Ferguson Co., Cleveland, whose engineers worked with those of the owner not only in developing the structures and building them but in improving, planning and installing the production equipment. Theodore K. Rothermund was project manager for the builder. Preparing the site Of first concern in the design were the foundation conditions. The entire site was found to be a fill, which had been placed to extend the old shoreline of the river about 400 ft. into the stream. Pile foundations, therefore, were necessary, and particularly so since the structures had to be designed for floor loads of from 250 to 2,000 lb. per sq.ft. Raymond step-tapered type concrete piles were chosen in order to assure maximum support in the Hudson River silt, and some 16,000 ft. of such piling was used. Most of the pile driving was relatively easy, but in the area of the can factory many large boulders were encountered which complicated the work considerably. Although basements are used in some of the buildings, none of them is excavated much below the prevailing ground level because of the soil conditions. Another item in site preparation was the construction of a steel bulkhead along the shoreline. Anchored to concrete sleepers, this bulkhead forms a wharf for tying up lighters that bring miscellaneous cargo to the === (page 74) [caption for photo top left] Fig. 2. Rolling cinder fill in a new pier structure built on top of existing timber piles 50 yr. old. --- plant. Considerable dredging followed construction of the bulkhead to make this wharf accessible. One of the most ambitious items of site preparation was the reconditioning of an old wooden pier, 60 ft. wide by 522 ft. long, built about 1888; a pier being an essential part of the plant, so that vessels, bringing green coffee from South America, can anchor and discharge their cargoes into storage. The old pier presented a very dilapidated appearance but the timber piling was found to be in good condition at and below mean tide level. The wooden superstructure, therefore, was torn down, and the piling cut off with an underwater saw 1 ft. below mean tide. On this cut-off piling a continuous decking of 6-in. plank was laid, and a reinforced gravity type retaining wall built on it around the perimeter of the pier. This retaining wall was to support a pier shed 68 ft. wide and in addition to retail a fill of clean boiler-house cinders upon which the reinforced concrete pier floor, designed for 600 lb. per sq.ft. live load, could be placed. The cinders were clam-shelled into place from a barge, spread in thin layers and compacted with heavy road rollers. Rebuilding of this old pier into a modern fire-resisting structure was one of the outstanding accomplishments of the project. The steel frame buildings Five of the seven buildings have steel frames, two of mill type and three of special type to fit particular requirements, and involving a total of 1,300 tons of structural steel. The mill-type buildings are the pier shed and the storage warehouse, both of clear span, 68 and 120 ft. respectively. The warehouse is 384 ft. long parallel to the shoreline and is equipped with a monitor roof. Side-walls and roofs of both buildings are of corrugated cement-asbestos sheets, although brick is used in the warehouse from foundation to window sills, and overhead counter-balanced steel doors inclose one side of the pier shed. Taken together, these two buildings provide storage for 20,000,000 lb. of green sacked coffee. Of the three other buildings, one, the laboratory, is a conventional 4-story tier-type structure, 70x170 ft. in plan, with timber floors, while the other two, the extraction building and the boiler house, have special functional frames. The extraction building was built to house the equipment necessary for removing the caffein from the green coffee bean, and contains four checker plate steel floors at various levels. It is 89 ft. wide and 214 ft. long and has a monitor roof. The boiler house, about 50x50 ft. in plan, is framed with clear-span trusses. Much of its interior steelwork is used to support the two oil-fired boilers. Roofs of these last two buildings are structural gypsum plank, while walls are solid brick, 12 in. thick— iron-spot brick on the exterior backed by sand-lime brick. Relieved by precast concrete sills and copings, these walls, which are also used on the coffee processing building and the can factory, give the plant an integrated appearance. The concrete frame buildings Heavy, large-scale manufacturing operations are confined to the 6-story processing building and the 4-story can factory, which are of reinforced concrete flat slab design, in panels 20 ft. square, with circular columns of a maximum diameter of 32 in. Floor slabs in the processing building are cantilevered 8 ft. beyond the column lines on the north and south walls. Both buildings accommodate a straight-line gravity-flow manufacturing operation. In the processing building, for example, coffee is received from the dock and warehouse into the east end of the basement and is carried by elevators to the roof, from where it flows by gravity through the cleaning, blending, roasting, grinding and packaging processes until it arrives on the first floor where railroad loading facilities are provided on the west elevation and truck loading facilities along the north elevation. In both buildings, too, access facilities are kept clear of the manufacturing floor by confining stairs, fire towers and elevators to outside enclosed shafts. The freight elevators, of which there are two of 12,000-lb. capacity in the processing building and one of 15,000-lb. capacity in the can factory, are equipped with micro-leveling devices that hold ---- [caption for photo bottom right] Fig. 3. As five steel frame and two concrete frame buildings for the coffee processing plant were being constructed simultaneously on a 9-acre site across the Hudson River from New York's skyscrapers. ---- ==== (page 75) the platform level with the floors under all conditions of loading. Of the two buildings, the processing building is the more simple since all of its floors are alike, being designed for 250 lb. per sq.ft. live load. One distinction that it has is provision for increasing its size by building up on the setbacks, the roofs of these setbacks being designed as future floors for full live load, while the columns for the future additions extend through the roof slabs as shown in Fig. 1. As roofs, the slabs are covered with a tar mastic sprinkled with slag. The factory for making the vacuum cans in which the company's coffees are packed is an unusual element of the plant. Adjoining the processing building on the west, it contains 113,245 sq.ft. of floor area and, as stated, is four stories high. Its reinforced concrete construction ends at the fourth floor and steel framing is used for the upper structure and the sawtooth monitor roof. In constructing this building every effort had to be made to avoid disturbing the piling foundation of the completed processing building. The columns adjoining this building bear on cantilever beams resting on two rows of pile caps at their inboard ends. This expedient made it possible to keep the can factory pile driving operations at a maximum distance from the processing building. There is no basement in the can factory, and the foundation walls were designed with tension ties to the interior pile caps so that they could retain a sand fill upon which the first floor is laid. This first floor slab is designed for a live load of 2,000 lb. per sq.ft. It is 7 in. thick, reinforced with 4 x 4 No. 2 gage welded wire mesh. At the expansion joints the slab thickness is increased to 9 in., and 1/2-in.-diameter dowels on 2-ft. centers run through the joints, which are filled with i-in. premolded mastic. The second and third floor slabs of the can factory are 10 1/2 in. thick and designed for a 300 lb. per sq.ft. live load. The first and second floors have a 3/4-in. cement finish, while a wood block wearing surface is used on the third and fourth floors, the latter being a 12 1/2-in. slab designed for 500 lb. per sq.ft. Roofs are gypsum planks. One of the unusual requirements in the can factory, as well as in the processing building, was provision of inserts and holes in the slabs for equipment. On the second floor of the can factory, for example, there are 550 inserts set in the ceiling for anchoring can bins, while in the third floor ceiling there are 2,560 of these inserts. All provisions for equipment anchorage and for pipes and inter-floor chutes were made in the original design, so that the forming and pouring of the floor slabs for these buildings was a complicated operation. This new coffee processing plant is now in full operation, and official dedication ceremonies were held on Oct. 13, with an "open house" celebration on the following day. [end] ==== Status: OK Status By: dw Status Date: 2012-10-22
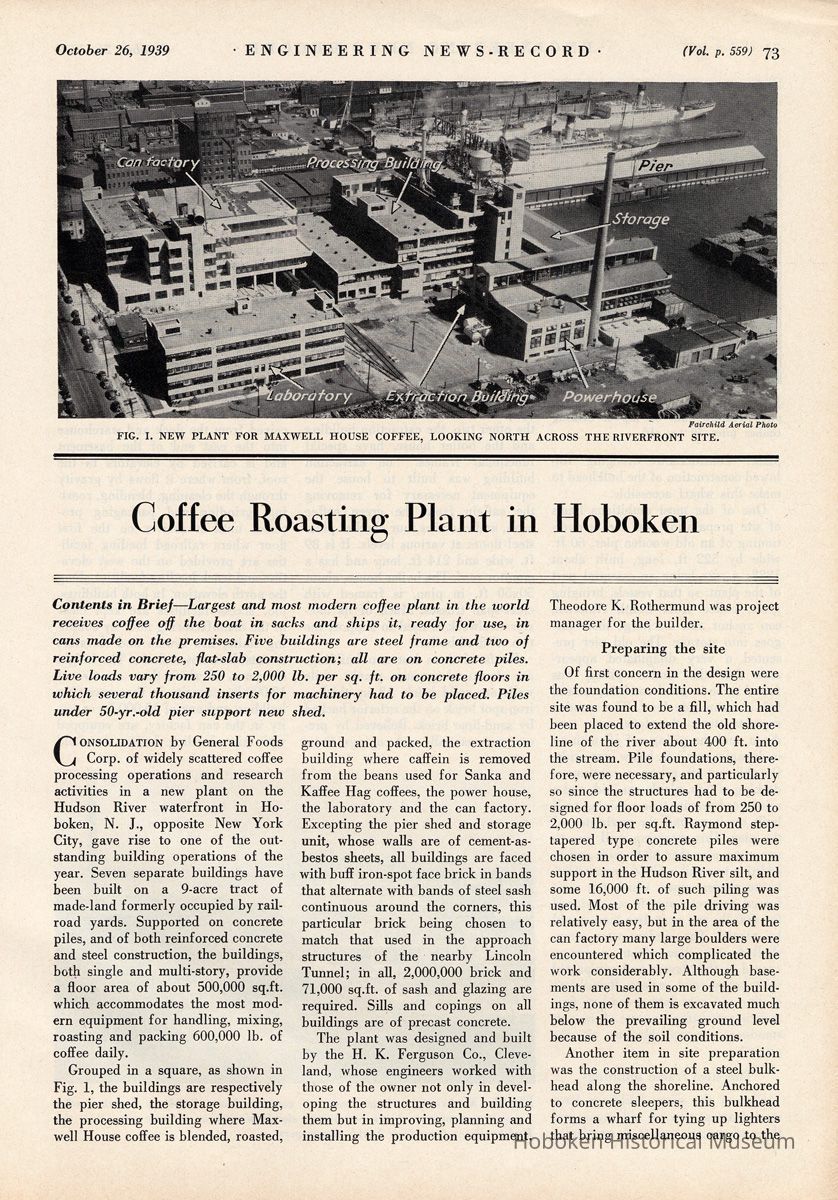