Article: "Hoboken Terminal Power Plant, D., L. & W., R.R." in The Railway & Engineering Review, May 9, 1908.
2009.006.0079
2009.006
Lukacs, Claire
Gift
Museum Collections. Gift of a friend of the Museum.
1908 - 1908
Date(s) Created: 1908 Date(s): 1908
Notes: Archives 2009.006.0079 THE RAILWAY AND ENGINEERING REVIEW May 9, 1908. Page 372 Hoboken Terminal Power Plant, D., W. & W. R. R. [Delaware, Lackawanna & Western Railroad] At the new terminal of the Delaware, Lackawanna & Western Railroad at Hoboken, N. J., which was put in service during last year, a new power plant is being installed for the purpose of furnishing electricity for light and power to all the Lackawanna properties in Hoboken. The location is just outside the end of the train shed of the new station and to the south of the entering tracks. This situation was chosen on account of its nearness to the terminal structures, so that the heat required for these buildings can be obtained economically from the power plant by utilizing the exhaust steam. The plant will also furnish live steam for beating coaches standing in the yard when not in use for the service during rush hours of the day. The power plant will contain compressors for furnishing the compressed air required to operate adjacent automatic track switches and signals well as for supplying such air-operated tools as may be used in the adjoining coach house and material building, where terminal cleaning and light repairs of every description are carried on.* *See Maintenance Facilities for Passenger Equipment. D., L & W. R. R. at Hoboken, Railway and Engineering Review, May 2, 1908, page 350. At the present time the plant is complete only as to the building and the setting of eight boilers, tour of which are in service. The foundations for the engine room equipment are now being placed and some of the smaller items of equipment are on hand but not yet in position. Architecturally the power house is a handsome structure of steel, brick and concrete. The dimensions are 94 ft. 8 ins, by 140 ft. 8 ins, and the interior is divided into three bays: Engine room, 40 ft. wide; boiler room, 35 ft. 8 ins.; coal pocket, 14 ft. An offset in the wall of the engine room 52 ft. 8 ins, long and '7 ft. 10 ins, deep affords room for the switchboard and the space in the rear is used for toilet facilities and other incidental purposes. Somewhat more than half of each of the two principal rooms is covered by a gallery constituting virtually a two-story building. The foundations are of concrete. The exterior walls are of brick on a framework of steel. The roof is carried on 84-inch lattice girders supported at the ends by the steel framework and by a row of intermediate steel columns encased in concrete, forming pillars 20 by 25 ins. The roof of the boiler room is carried about 10 feet higher than the rest of the building and this part of the roof is carried on 38-inch lattice girders. Two monitors with louvres occupy about three-fourths the length of the building over the boilers. The gallery floors are of concrete 6 ins, thick, carried on 21-inch plate girders at the vertical columns and reinforced with 6-inch I-beams spaced ordinarily 16 ft. 6 1/2 ins, apart. In connection with this floor is' built the curbing for the Green fuel economizers, 24 1/2 ins, high and 8 ins, thick. The edges of the gallery throughout are protected by an iron pipe railing. The lower part of the coal pocket is entirely of concrete with 18-inch outer and 16-inch inner wall. Between each two of the roof-supporting columns which are spaced 16% ft. are openings from the coal pocket to the boiler room through which coal is delivered to the boiler room floor. 'By means of a trestle outside loaded cars are run in upon the second floor of the coal pocket and the contents dumped. An ash-conveyor running on an overhead trolley in the space in front of the boilers provides means for the removal of ashes which are carried by the same trolley over a delivery track on the ground level alongside the coal trestle, whence they are dumped into cars. In the boiler room the equipment consists of 8 boilers, 306 horsepower each, made by the Atlas Engine Works, which will operate at a working pressure of 150 pounds per square inch. Each boiler contains 3062 square feet of heating surface and 80% square feet of grate surface, the grates being 11 feet 6 inches wide and 7 feet deep. The boilers are installed under a. guarantee to furnish steam at from 30 to 40 degrees F. of superheat at all loads. The boilers are equipped with Williams feed water regulators and the Parson Manufacturing Co. system of pinhole grates and steam blowers. This equipment is designed to burn anthracite coal, barley size. The stack, 8 ft. in diameter, of steel, and rising to a bight of 60 ft. above the grates, is provided simply for the purpose of carrying off the gases. After leaving the boiler the gases are conducted by means of a steel breeching and flues to economizers furnished by the Green Fuel Economizer Co. These are set in two banks and contain in all 6969 square feet of heating surface. Each economizer is composed of 40 sections Page 373 and each section is 8 tubes deep. After passing through the economizers the gases pass through fans the blast wheels of which have a diameter of 9 feet and a width of 51 1/2 inches, and thence to the stack. Suitable dampers are provided in the flues and fan housings to permit the gases leaving the boilers to go through the economizers and thence through both or either of the fans; or to permit short-circuiting the economizers entirely so that the gases go directly to the stack through either or both of the fans. The fans are direct-connected to 9 by 12-in. horizontal engines manufactured by the Atlas Engine Works. Scrapers for removing the soot from the outer surfaces of the economizer tubes are operated by a 5-horsepower induction motor. Owing to the character of the fuel to be used it is expected that it will probably not be necessary to operate the scrapers continuously. Ashes are drawn from the firing door into a steel bucket, which is hoisted and conveyed out of the building by means of an electrically operated hoist and conveyor, manufactured by the Sprague Electric Co. The hoist is provided with a magnetic trip attachment so that ashes may be dumped into any predetermined part of a train of cars. After the bucket is filled all that is necessary for the fireman to do is to throw a switch which causes the hoist to lift the bucket to a point about 12 feet above the boiler room floor. He then throws another switch and the hoist with the bucket travels out of the building to the point where it is desired to dump the contents. The bucket trips automatically and hoist and bucket return to the boiler room. In the boiler room will be provided a room with lockers for firemen's clothing and space for toilet and lavatory accommodations. In the turbine room, separated from the boiler room by a brick wall, are to be installed two steam-driven boiler feed pumps. These are 14 by 8 by 12-in, duplex outside-packed pot-valve plunger Knowles pumps, either of which is of sufficient size to supply water to the boilers. They will be automatically regulated by two 2 1/2-in. Fulton steam pump governors, piston type, manufactured by the Chaplain-Fulton Manufacturing Co. Water is brought into the building through two 8-in, pipes taking supply from independent pipe lines. From the pumps the water is piped to a 2400-horsepower open-type Cochrane feed-water heater and purifier. The piping is of course so arranged as to by-pass when necessary to clean the heater. From the heater the water is taken to the economizers and thence to the boilers, provision being made to by-pass the economizers when desirable. Exhaust steam is supplied to the feed-water heater from the boiler-feed pumps, engine-driven exciter, the engines driving the blower fans; and the heater is also so arranged that it may obtain the exhaust steam from the compressors. The switchboard, which was built by the General Electric Co., is of blue Vermont marble. It consists of one synchronizer mounted on a bracket; one 2-circuit exciter panel; one 3-phase induction motor and T. A. regulator panel; two 500-kilowatt, 3-phase generator panels; two blank 3-phase generator panels; seven 3-phase feeder panels for light and power circuits; two constant-current trans-former panels each for controlling a 50-light, 7%- ampere secondary oil-cooled "tub" transformer, General Electric make; one 3-phase ground detector on swinging bracket. The switchboard is mounted directly on the front of the columns of the building, the necessary blank panels are provided to stand in front of the columns. It is provided with all the usual or necessary indicating and recording instruments. Its location is opposite an offset in the wall of the building so that the front of the switchboard will be flush with the inside of the wall and the apparatus at the back will be in the offset. Turbines, motor-driven exciter and switchboard will be located on the gallery. Underneath the switchboard gallery will be located the "tub" transformers and space is provided for feeder circuits leaving the building under ground. Under the switchboard and in the offset space is provided for lockers, toilet and washroom for the engine-men. With each turbine will be provided one Worthington surface-condenser of 2000 sq. ft. surface, provided with brass tube heads and tubes; one Worthington 6 by 10 by 12-in, horizontal straight- line rotation dry-vacuum pump; one Worthington 8-in, horizontal volute centrifugal circulating pump direct-connected to and on a common bed-plate with one 6 by 7-in. Westinghouse standard engine, the combined unit to be capable of delivering a maximum capacity of 1800 U. S. gallons per minute against a head of 20 ft. based on syphon circulation. With each condenser, to remove the water of condensation, is provided one Worthington 1 1/2-in. horizontal two-stage turbine centrifugal hot-well pump furnished with extended bed-plate and direct- connected to a 440-volt three-phase Westinghouse Electric & Manufacturing Co.'s induction motor. This pump has a maximum capacity of 20,000 pounds of steam per hour delivering against a total head of 25 ft. when operating at 1690 revolutions per minute. Each condenser unit is capable of condensing 12,000 pounds of steam per hour, maintaining a vacuum of 28 ins, based on a 30-in. barometer, and provided with sufficient circulating water at a temperature not exceeding 70 degrees F. Salt water, used for circulation, is piped to a well in the building through a 24-in, inside diameter concrete pipe, the center of which is installed 9 ft. below mean tide or 4 ft. below lowest tide-water mark. There is a suitable screen chamber at the intake. Condensed steam is piped directly to the boiler feed-water heater. The circulating water, after passing through the condenser, is piped into another well which discharges to the river. The piping is carried down so that its end is always sealed in order to assure syphoning action and thus relieve the load on the engines driving the circulating pumps. The exhaust piping from the turbines is so arranged that the steam goes directly to the above-mentioned condenser system, or it may be taken to an exhaust feed-water heater for heating the water required for heating the building page 374 In the same room will also be installed three steam-driven compressors. Two of these are old compressors which will be transferred to this building from the old plant. They are exact duplicates designed for duplex steam, non-condensing, compound air, The diameter of the steam cylinder is 12 ins.; low pressure air, 18 ins.; high pressure air, 11 ins.; stroke, 16 ins. Each has a capacity of 565 cu. ft. of free air per minute when operating at 120 revolutions per minute. The third compressor is a new one, cross-compound steam and air with Corliss cut-off. The air cylinders are 25 and 15 by 20 ins.; steam cylinders, 12 and 28 by 30 ins. This compressor has a capacity of 1700 Cu. ft. of free air per minute when operating at a speed of 150 revolutions per minute. There is an intercooler between the two air cylinders. The compressor is suitable for operating non-condensing or condensing. The foundation of one of the smaller compressors is so constructed that if it shall be found desirable at some future time to enlarge the compressor capacity, a second compressor the duplication of the larger one now being installed can be readily mounted in its place. It is expected that the larger compressor will readily be able to take care of the maximum loads and that the smaller compressors will be used only on very light loads or at such times as repairs may be required by the larger one. Piping is so arranged that exhaust steam may be taken direct to the boiler feed-water heater or by-passed to the atmosphere. One of the smaller compressors and the larger compressor may be piped to the exhaust heater used for heating the water required by the hot-water building heating system, or the exhaust heater can be by-passed and connected back to the condensors which are primarily installed for the turbines. After leaving the compressors the compressed air will be taken to a water-cooled after cooler and then piped under ground through mains running throughout the yard. Provision is also made for the installation of two 1500-gallon Underwriters' steam-driven fire pumps, only one of which will be installed at present. These pumps will handle salt water. The auctions are carried down into a well located directly in front of the pumps and this well is connected by means of a concrete pipe to the well from which the condenser circulating pumps obtain their water. Reference has been made to the heating system of the terminal station. This is what is known as the Evans-Almirall system of hot-water heating by exhaust steam. The circulating water is carried through 10-in, pipes to the terminal station and std3acent buildings. It is passed through the exhaust heater already mentioned, thence through one of two circulating pumps, one outfit consisting of a DeLaval gearless pump direct-connected to an induction motor and the other consisting of a DeLaval gearless pump direct-connected to a DeLaval steam turbine. The water is then carried to the top of the boiler room where, in case there is not enough exhaust steam in the exhaust heater to heat the water to the required temperature, it may be passed through a live-steam heater and thence out of the building. Suitable valves are placed so that the heater and pumps may be bypassed and an expansion tank is furnished. The exhaust steam connections to the exhaust steam heater are such that the steam from either or both turbines and compressors may be taken directly to the exhaust heater and thence to the Worthington condensers, permitting the exhaust steam to be under a vacuum. The colder the weather the lower the vacuum and the warmer the weather the higher the vacuum, thus varying the temperature of the steam in the exhaust heater to meet the heating requirements. Steam for the live steam heater is obtained from the live steam header in the boiler room. The condensed steam from the exhaust steam heater is piped to a two-stage turbine pump, a duplicate of those used for removing water from the turbines and is pumped directly to the feed-water heater. These three 2-stage pumps are so connected that in case of trouble to any one of them the other two may take its load. The condensed steam from the live-steam heater is carried back into the boilers by gravity. All of the piping for the building is being furnished by the M. W. Kellogg Co. The high-pressure steam and hot-water circulating piping has the Vanstone type of joints and flanges. The high- pressure steam valves are of New Bedford make. All boiler feed-water piping is extra heavy wrought iron. The piping for salt water is of cast iron. The high-pressure steam header makes an entire loop of the boiler and turbine rooms. The boilers are connected to it through New Bedford non-return and globe valves. Connections are taken from the header to the several turbines and auxiliary apparatus and an 8-in, line is carried from it out of the building to the underground steam line which has connections for use in supplying heat to coaches standing in the yard. All fittings in the steam line, with the exception of special cast steel fittings in the branches, are of extra heavy cast iron. The special fittings are so designed as to take steam from the top of the header and act as separators. A Holley system is installed to take care of condensation and moisture in the steam line, the water of condensation being returned to the boilers. Open blows are installed on leads from all boilers to the header so that when working on a boiler they may be opened and it will be impossible to get up a pressure of steam against the non-return valve without the attendant being aware of the fact. The open blows also prevent an accumulation of water in the pipes. Open blows are also installed at other points, so that they may be opened to the atmosphere when any section of the steam piping is shut off. In the turbine room is installed a 6-ton hand traveling crane built by Maris Brothers and having a span of 28 ft. 6 ins. The room is so designed that it is possible to handle nearly all of the machinery by means of the crane. As before stated, coal is delivered in cars to the second floor of the pocket and ashes are removed by a trolley conveyor and dumped in cars outside. The construction and arrangement of this part of the plant are of considerable interest. The trestle approach to the coal pocket is entirely of concrete and lies alongside the material building and coach house used by the car department. This structure is also made to serve as a support upon one side of the steel structure which carries the trolley track of the ash-conveyor and some modifications have been introduced into the plan of the trestle on account of the double purpose served. The ash track lies between the trestle approach and the material building of the car department. The trolley track and its supporting structure extend for 130 ft. from the power house. The length of the trestle proper is 226 ft., and it is made up of 18 bents on piers 12 ft. apart. One of the abutments is the wall of the coal pocket and the other is the extremity of an approach 112 ft. 4 ins., in length made up of concrete walls filled in. The retaining walls are tied together by old rails extending from one to the other and secured in each by an 18-in, rod embedded in the concrete. The grade is 4 per cent up to within two or three bents of the entrance to the power-house where a vertical curve is introduced to bring the rails to a level. About one-half of the whole width of the structure, 16 ft., is occupied by a walk on each side of the track. All the piers are supported upon piles, the site being largely made ground. The footings are 4 ft. 9 ins, in width and vary in length from 11 ft. 9½ ins, to 13 ft. according to the light. Each pier is 10 ft. wide and batters from the footing to a uniform thickness of 18 ins, at the top. These carry the stringers, which are 18 ins., in width and 27 ins, deep. In them are embedded 12 by %-iu. bolts holding the clamps for securing the rails. The rails rest directly upon the stringers without the interposition of a steel bearing plate, as is customary, though the bolts are long enough to admit of the insertion of plates if it should be found desirable. In order to separate from the rest of the structure any strains that might be induced by a load upon the stringers the space between them and the side walks has been left open. They also serve as dumping spaces whenever it is desired to dump material therefrom. The piers are reinforced by 3/4-in. square rods placed vertically in two rows near the outside, spaced 5 ins, apart under the stringers and 8 ins. elsewhere, and by horizontal rods 18 ins, apart. The stringers have a reinforcement of three 114 in. rods three inches from the bottom and tension reinforcement over bearing points by similar rods 8 ft. 4 ins., long. These rods also support over each pair an inverted rail extending the whole width of the structure and forming the principal Page 375 support of the side walks. The rails are connected by rods attached thereto by clips which embrace the rail head and on this basis the concrete walk is bunt. On the side away from the material building no other support is required for the side walk, but on the 'inside, as the same rails also support the uprights of the trolley structure, additional strength is given by a bracket under each rail. The opposite ends of the beams supporting the trolley are carried by the wall of the material building. It will be noticed that the necessity of compactness has been kept in view throughout. In the approach part uf the coal trestle the retaining walls could have been dispensed with and the filling allowed to take a natural slope were it not for the fact that the ground close up on either side is occupied by tracks in frequent service. The plant was designed, erected and is being equipped under the direction of the engineering department of the Lackawanna Railroad, Lincoln Bush, chief engineer, George T. Hand, assistant engineer, F. J. Nies, architect. The equipment has been the especial charge of H. M. Warren, electrical engineer, to whom we are indebted for the details of the installation covered in the foregoing description. [end article] --------------------- Partial article found on page 376 The Hudson & Manhattan Railroad.* The Hudson & Manhattan Railroad system will when completed comprise about 19 miles of tunnel, of which six miles are now in operation and six additional miles of tunnel are completed ready for concrete sidewalls, ballast and track. By the end of the year it is expected that about 16 miles of tunnel will he completed and in operation. The line now in operation begins at Hoboken where a terminal station is placed adjacent to the Delaware, Lackawanna & Western Railroad station, and from this point cars run to 19th street and Sixth avenue, New York City. The Sixth avenue line will be extended eventually to 33rd street, where a terminal will he built. On the New Jersey side a station will be placed adjacent to the Erie Railroad station; there also will be a station directly below the Pennsylvania Railroad station. There are two downtown tunnels that cross under the river between the Pennsylvania Railroad station and Cortlandt street, and the terminal station for these downtown tunnels is located on Church street between Cortlandt and Fulton streets. This terminal is located so as to be within convenient distance of the business portion of the city. The terminal at 33rd street and the stations up Sixth avenue furnish convenient access to the shopping district, so that when the road is completed a passenger, either from the Lackawanna, Erie or Pennsylvania railroad, or from trolley lines at Hoboken or Jersey City, can ride under the river directly to the shopping district along Sixth avenue, or to the heart of the business district near the Church street terminal. A pair of tunnels are to run west under the Pennsylvania right of way to a point about two miles west of the Pennsylvania Railroad station at Summit avenue, where the tunnels come to the surface and the tracks will connect to the Pennsylvania tracks. There is a traffic arrangement between the Pennsylvania Railroad and the Hudson & Manhattan Railroad, whereby the Pennsylvania local trains [end of available text] * Extracts from discussion by Hugh Hazleton before the New York Railroad Club, March 20, 1908. Status: OK Status By: dw Status Date: 2009-06-11
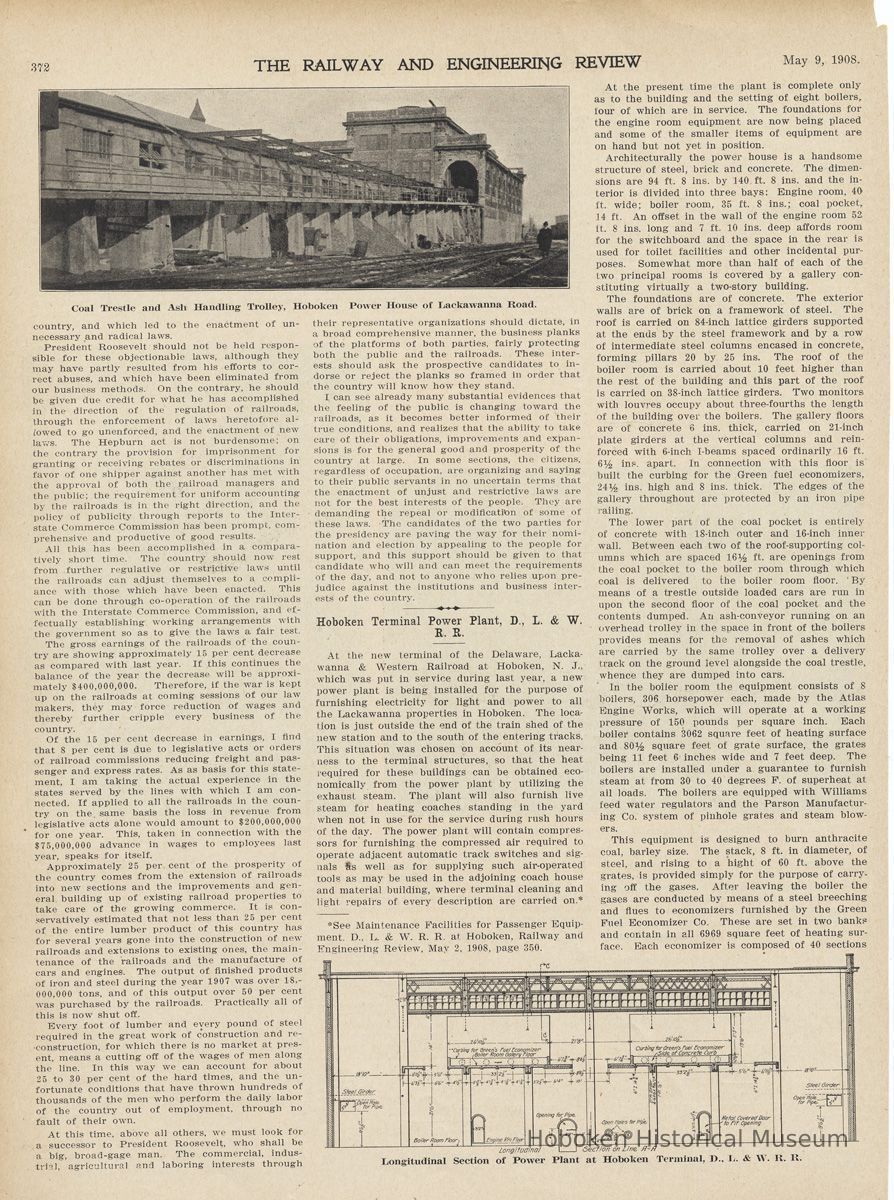